Destylator przemysłowy to urządzenie służące do oddzielania składników cieczy na podstawie różnicy w ich temperaturach wrzenia. Proces ten jest kluczowy w wielu branżach, takich jak chemiczna, petrochemiczna czy spożywcza. W destylacji wykorzystuje się zjawisko parowania i skraplania, co pozwala na efektywne rozdzielenie substancji. Destylatory przemysłowe mogą mieć różne formy, w tym kolumnowe, prostokątne czy wirnikowe, a ich wybór zależy od specyfiki produkcji oraz rodzaju przetwarzanych cieczy. W praktyce, proces destylacji polega na podgrzewaniu cieczy do momentu, gdy zaczyna ona parować, a następnie schładzaniu pary, co prowadzi do jej kondensacji i zbierania w postaci czystego produktu. Dzięki temu możliwe jest uzyskanie wysokiej czystości substancji, co ma kluczowe znaczenie w wielu zastosowaniach przemysłowych.
Jakie są rodzaje destylatorów przemysłowych i ich zastosowanie
W przemyśle można spotkać różne rodzaje destylatorów, które różnią się konstrukcją oraz zastosowaniem. Najpopularniejsze z nich to destylatory prostoliniowe, kolumnowe oraz wirnikowe. Destylatory prostoliniowe są najprostsze w budowie i najczęściej stosowane w małych zakładach produkcyjnych. Działają na zasadzie jednofazowego procesu destylacji, gdzie ciecz jest podgrzewana w jednym zbiorniku. Z kolei destylatory kolumnowe charakteryzują się bardziej skomplikowaną budową i umożliwiają wielokrotne skraplanie pary, co pozwala na uzyskanie wyższej czystości produktów. Są one powszechnie stosowane w dużych zakładach chemicznych oraz rafineriach. Destylatory wirnikowe natomiast wykorzystują siłę odśrodkową do separacji składników cieczy i są stosowane głównie w przemyśle spożywczym oraz farmaceutycznym.
Jakie są zalety korzystania z destylatorów przemysłowych
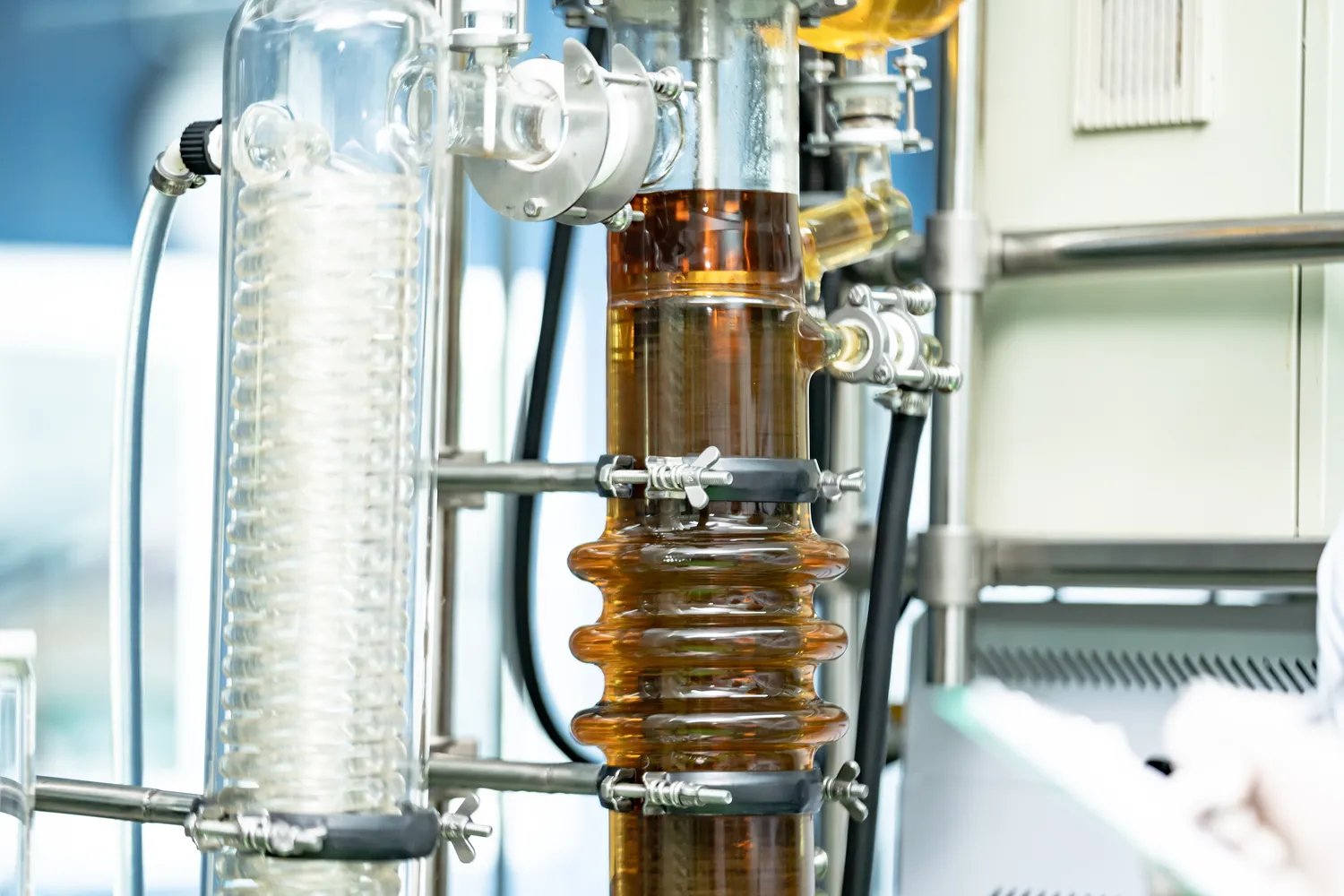
Korzystanie z destylatorów przemysłowych niesie ze sobą wiele korzyści dla producentów oraz całego sektora przemysłowego. Przede wszystkim umożliwiają one uzyskanie wysokiej czystości produktów końcowych, co jest niezwykle istotne w branżach wymagających spełnienia rygorystycznych norm jakościowych. Dzięki efektywnemu rozdzielaniu składników cieczy można również zoptymalizować procesy produkcyjne, co prowadzi do oszczędności czasu i kosztów. Kolejną zaletą jest możliwość automatyzacji procesów destylacyjnych, co zwiększa wydajność i redukuje ryzyko błędów ludzkich. Warto również wspomnieć o elastyczności destylatorów – wiele modeli można dostosować do różnych rodzajów cieczy oraz zmieniających się warunków produkcji. Dzięki temu przedsiębiorstwa mogą szybko reagować na zmiany popytu oraz dostosowywać swoje procesy do aktualnych potrzeb rynku.
Jakie są wyzwania związane z użytkowaniem destylatorów przemysłowych
Pomimo licznych zalet korzystania z destylatorów przemysłowych istnieją także pewne wyzwania związane z ich użytkowaniem. Jednym z głównych problemów jest konieczność regularnej konserwacji i czyszczenia urządzeń, aby zapewnić ich prawidłowe działanie oraz uniknąć kontaminacji produktów końcowych. Z czasem osady mogą gromadzić się wewnątrz kolumn czy zbiorników, co wpływa negatywnie na efektywność procesu destylacji. Kolejnym wyzwaniem jest kontrola parametrów procesu, takich jak temperatura czy ciśnienie, które muszą być ściśle monitorowane dla zapewnienia optymalnych warunków pracy urządzenia. Niewłaściwe ustawienia mogą prowadzić do obniżenia jakości produktów lub nawet uszkodzenia sprzętu. Dodatkowo inwestycje w nowoczesne technologie mogą być kosztowne dla mniejszych przedsiębiorstw, które nie zawsze dysponują odpowiednimi środkami finansowymi na modernizację swoich linii produkcyjnych.
Jakie są najnowsze technologie w destylacji przemysłowej
W ostatnich latach rozwój technologii związanych z destylacją przemysłową znacząco wpłynął na efektywność i jakość procesów produkcyjnych. Nowoczesne destylatory wykorzystują zaawansowane systemy automatyzacji, które pozwalają na precyzyjne kontrolowanie parametrów pracy, takich jak temperatura, ciśnienie czy przepływ. Dzięki zastosowaniu czujników i systemów monitorujących, operatorzy mogą na bieżąco śledzić przebieg procesu i wprowadzać niezbędne korekty, co zwiększa wydajność oraz minimalizuje ryzyko błędów. Warto również zwrócić uwagę na rozwój technologii membranowych, które stanowią alternatywę dla tradycyjnych metod destylacji. Membrany umożliwiają separację składników cieczy na podstawie ich wielkości cząsteczkowej, co może być korzystne w przypadku substancji wrażliwych na wysokie temperatury. Kolejnym innowacyjnym rozwiązaniem są destylatory z odzyskiem energii, które pozwalają na wykorzystanie ciepła generowanego w procesie do podgrzewania kolejnych partii cieczy, co znacząco obniża koszty operacyjne.
Jakie są kluczowe czynniki wpływające na wybór destylatora przemysłowego
Wybór odpowiedniego destylatora przemysłowego to proces wymagający uwzględnienia wielu czynników, które mogą mieć istotny wpływ na efektywność produkcji. Przede wszystkim należy określić rodzaj cieczy, która będzie poddawana destylacji, ponieważ różne substancje mogą wymagać różnych parametrów pracy oraz konstrukcji urządzenia. Kolejnym istotnym aspektem jest skala produkcji – małe zakłady mogą potrzebować prostszych i tańszych rozwiązań, podczas gdy duże przedsiębiorstwa powinny inwestować w bardziej zaawansowane technologie kolumnowe lub wirnikowe. Koszt zakupu oraz eksploatacji urządzenia to również kluczowy element decyzji, który powinien być dokładnie przeanalizowany w kontekście budżetu firmy. Nie można zapominać o aspektach związanych z konserwacją i serwisem – wybierając destylator warto zwrócić uwagę na dostępność części zamiennych oraz wsparcie techniczne ze strony producenta.
Jakie są zastosowania destylatorów przemysłowych w różnych branżach
Destylatory przemysłowe znajdują szerokie zastosowanie w wielu branżach, co czyni je niezwykle wszechstronnymi urządzeniami. W przemyśle chemicznym są one wykorzystywane do produkcji różnorodnych substancji chemicznych, takich jak alkohole, kwasy czy rozpuszczalniki. Proces destylacji pozwala na uzyskanie wysokiej czystości produktów, co jest kluczowe dla dalszego przetwarzania. W branży petrochemicznej destylatory odgrywają fundamentalną rolę w rafinacji ropy naftowej – dzięki nim możliwe jest oddzielanie poszczególnych frakcji paliwowych oraz innych produktów pochodnych. W przemyśle spożywczym destylacja jest stosowana do produkcji napojów alkoholowych, takich jak whisky czy wódka, gdzie jakość i czystość końcowego produktu mają ogromne znaczenie dla konsumentów. Również w farmaceutyce proces ten jest niezbędny do uzyskania substancji czynnych o wysokiej jakości.
Jakie są koszty związane z eksploatacją destylatorów przemysłowych
Koszty eksploatacji destylatorów przemysłowych mogą być znaczne i powinny być dokładnie analizowane przed podjęciem decyzji o zakupie konkretnego urządzenia. Do głównych wydatków należy zaliczyć koszty energii potrzebnej do podgrzewania cieczy oraz chłodzenia pary podczas procesu destylacji. W zależności od rodzaju używanego paliwa lub energii elektrycznej, te wydatki mogą znacząco wpłynąć na całkowity koszt operacyjny zakładu. Kolejnym istotnym elementem są koszty konserwacji i serwisowania urządzeń – regularne przeglądy oraz ewentualne naprawy są niezbędne dla zapewnienia ciągłości produkcji oraz uniknięcia awarii. Dodatkowo warto uwzględnić koszty związane z zakupem surowców oraz materiałów eksploatacyjnych, takich jak chemikalia do czyszczenia czy części zamienne.
Jakie są przyszłe kierunki rozwoju technologii destylacyjnej
Przemysłowa technologia destylacyjna stale ewoluuje i dostosowuje się do zmieniających się potrzeb rynku oraz wymogów środowiskowych. W przyszłości można spodziewać się dalszego rozwoju systemów automatyzacji i monitorowania procesów, co pozwoli na jeszcze większą precyzję oraz efektywność działania destylatorów. Technologie odzysku energii będą coraz bardziej popularne, a ich implementacja stanie się standardem w nowoczesnych zakładach produkcyjnych. Również rozwój materiałów odpornych na korozję i wysokie temperatury przyczyni się do zwiększenia trwałości urządzeń oraz obniżenia kosztów eksploatacyjnych. W kontekście ochrony środowiska można oczekiwać wzrostu zainteresowania ekologicznymi metodami separacji substancji chemicznych, takimi jak ekstrakcja cieczy czy membrany filtracyjne, które mogą stanowić alternatywę dla tradycyjnej destylacji. Ponadto rosnące zainteresowanie produktami naturalnymi oraz zdrowotnymi może prowadzić do rozwoju nowych aplikacji dla technologii destylacyjnej w branży spożywczej i farmaceutycznej.
Jakie są najczęstsze błędy przy użytkowaniu destylatorów przemysłowych
Użytkowanie destylatorów przemysłowych wiąże się z pewnymi ryzykami, a niektóre błędy mogą prowadzić do poważnych konsekwencji. Jednym z najczęstszych problemów jest niewłaściwe ustawienie parametrów pracy, takich jak temperatura i ciśnienie, co może skutkować obniżoną jakością produktów lub uszkodzeniem urządzenia. Kolejnym błędem jest brak regularnej konserwacji, co prowadzi do gromadzenia się osadów i zmniejszenia efektywności procesu. Niedostateczne szkolenie personelu obsługującego destylatory również może przyczynić się do wystąpienia awarii. Warto również pamiętać o konieczności monitorowania jakości surowców, ponieważ zanieczyszczenia mogą negatywnie wpłynąć na końcowy produkt.