Destylacja rozpuszczalników to proces, który polega na oddzieleniu składników mieszaniny na podstawie różnicy ich temperatur wrzenia. W praktyce oznacza to, że ciecz o niższej temperaturze wrzenia paruje jako pierwsza, a następnie skrapla się w chłodnicy, tworząc czystszy produkt. Proces ten jest szeroko stosowany w chemii, przemyśle farmaceutycznym oraz w produkcji alkoholu. Kluczowym elementem destylacji jest zastosowanie odpowiednich urządzeń, takich jak kolumny destylacyjne, które zwiększają efektywność separacji poprzez wielokrotne skraplanie i parowanie. Warto również zaznaczyć, że destylacja może być przeprowadzana na różne sposoby, w tym destylację prostą, frakcyjną oraz destylację pod ciśnieniem. Każda z tych metod ma swoje specyficzne zastosowania i jest dostosowana do rodzaju substancji, które mają być oddzielone.
Jakie są rodzaje destylacji rozpuszczalników i ich zastosowania
W kontekście destylacji rozpuszczalników wyróżniamy kilka głównych rodzajów, które różnią się zarówno techniką wykonania, jak i zastosowaniem. Destylacja prosta jest najstarszą i najłatwiejszą formą tego procesu, stosowaną głównie do oddzielania substancji o znacznie różniących się temperaturach wrzenia. W przypadku mieszanin, gdzie składniki mają zbliżone temperatury wrzenia, lepszym rozwiązaniem jest destylacja frakcyjna. Ta metoda wykorzystuje kolumny destylacyjne, które umożliwiają wielokrotne skraplanie i parowanie, co prowadzi do uzyskania wyższej czystości produktu końcowego. Kolejnym rodzajem jest destylacja pod ciśnieniem, która pozwala na obniżenie temperatury wrzenia substancji i jest szczególnie przydatna w przypadku termolabilnych związków chemicznych. Wybór odpowiedniej metody zależy od charakterystyki mieszaniny oraz pożądanej czystości końcowego produktu.
Jakie są kluczowe etapy procesu destylacji rozpuszczalników
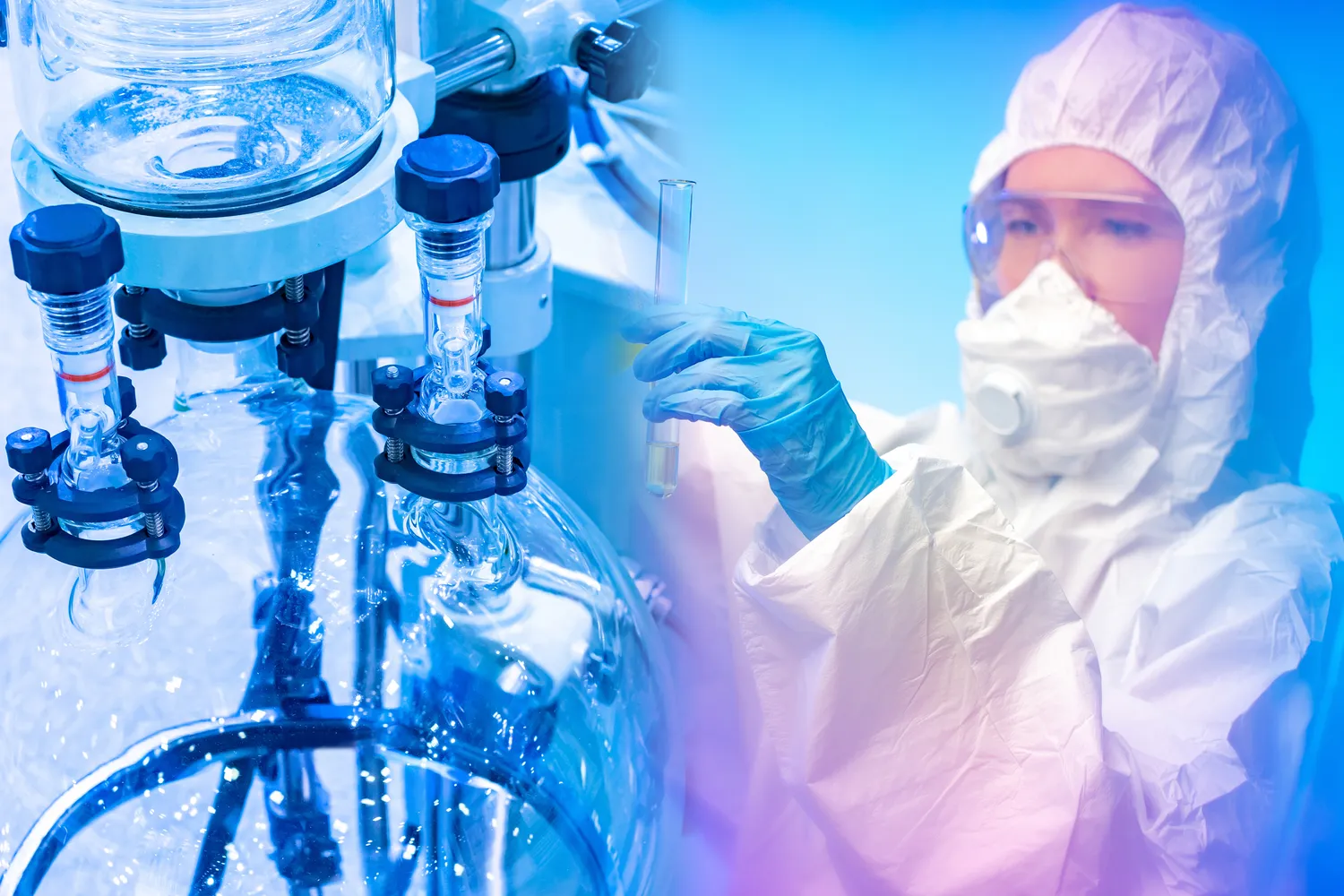
Proces destylacji rozpuszczalników można podzielić na kilka kluczowych etapów, które są niezbędne do uzyskania pożądanego efektu separacji. Pierwszym krokiem jest przygotowanie mieszaniny do destylacji, co często obejmuje filtrację lub oczyszczanie surowców. Następnie następuje podgrzewanie mieszaniny w kolbie grzewczej, co powoduje parowanie składników o niższej temperaturze wrzenia. Para ta przemieszcza się do chłodnicy, gdzie ulega skropleniu i zbiera się w osobnym naczyniu. Ważnym aspektem tego etapu jest kontrola temperatury oraz ciśnienia, ponieważ wpływają one na wydajność całego procesu. Po skropleniu następuje analiza uzyskanego produktu pod kątem czystości oraz zawartości poszczególnych składników. W przypadku konieczności dalszego oczyszczania można powtórzyć proces destylacji.
Jakie są najczęstsze błędy podczas destylacji rozpuszczalników
Podczas przeprowadzania procesu destylacji rozpuszczalników mogą wystąpić różnorodne błędy, które wpływają na jakość uzyskanego produktu oraz efektywność całej operacji. Jednym z najczęstszych problemów jest niewłaściwe ustawienie temperatury grzania, co może prowadzić do niepełnej separacji składników lub ich degradacji. Kolejnym błędem jest zbyt szybkie podgrzewanie mieszaniny, co może skutkować powstawaniem piany i utratą cennych substancji w postaci aerozoli. Niewłaściwe dobranie kolumny destylacyjnej lub jej niewystarczająca wysokość również mogą wpłynąć negatywnie na efektywność separacji. Ponadto ważne jest zachowanie odpowiednich warunków pracy urządzeń oraz regularne ich czyszczenie i konserwacja. Ignorowanie tych aspektów może prowadzić do zanieczyszczenia produktu końcowego oraz obniżenia wydajności procesu.
Jakie są najważniejsze zastosowania destylacji rozpuszczalników w przemyśle
Destylacja rozpuszczalników odgrywa kluczową rolę w wielu gałęziach przemysłu, a jej zastosowania są niezwykle różnorodne. W przemyśle chemicznym proces ten jest wykorzystywany do oczyszczania surowców oraz produkcji wysokiej czystości substancji chemicznych. Na przykład, w produkcji alkoholu destylacja jest niezbędna do uzyskania czystego etanolu z fermentacji. W przemyśle farmaceutycznym destylacja służy do separacji i oczyszczania aktywnych składników leków, co jest kluczowe dla zapewnienia ich skuteczności i bezpieczeństwa stosowania. Również w przemyśle petrochemicznym destylacja frakcyjna jest podstawowym procesem w rafinacji ropy naftowej, gdzie różne frakcje są oddzielane w zależności od ich temperatur wrzenia. Dodatkowo, destylacja znajduje zastosowanie w produkcji kosmetyków, gdzie czyste olejki eteryczne są pozyskiwane z roślin.
Jakie są nowoczesne technologie stosowane w destylacji rozpuszczalników
W ostatnich latach rozwój technologii przyczynił się do znacznej poprawy efektywności procesu destylacji rozpuszczalników. Nowoczesne urządzenia, takie jak kolumny destylacyjne o wysokiej efektywności, pozwalają na lepsze wykorzystanie energii oraz zwiększenie wydajności separacji. Wprowadzenie automatyzacji i systemów monitorowania umożliwia precyzyjne kontrolowanie parametrów procesu, takich jak temperatura i ciśnienie, co przekłada się na wyższą jakość uzyskiwanych produktów. Ponadto, technologie takie jak destylacja membranowa czy ekstrakcja cieczy cieczą stają się coraz bardziej popularne jako alternatywy dla tradycyjnej destylacji. Te innowacyjne metody mogą oferować mniejsze zużycie energii oraz lepsze wyniki separacji w przypadku niektórych mieszanin. Również rozwój materiałów odpornych na wysokie temperatury i korozję przyczynia się do zwiększenia trwałości urządzeń stosowanych w procesie destylacji.
Jakie są wymagania dotyczące bezpieczeństwa podczas destylacji rozpuszczalników
Bezpieczeństwo podczas przeprowadzania procesu destylacji rozpuszczalników jest niezwykle istotne ze względu na potencjalne zagrożenia związane z używanymi substancjami chemicznymi oraz wysokimi temperaturami. Przede wszystkim ważne jest stosowanie odpowiednich środków ochrony osobistej, takich jak rękawice, gogle ochronne oraz odzież robocza odporna na chemikalia. Należy również zapewnić odpowiednią wentylację w pomieszczeniu, aby uniknąć gromadzenia się szkodliwych oparów. Kolejnym kluczowym aspektem jest regularne sprawdzanie stanu technicznego urządzeń wykorzystywanych w procesie destylacji, aby zapobiec awariom i wyciekom substancji chemicznych. Ważne jest również przestrzeganie procedur awaryjnych oraz znajomość lokalnych regulacji dotyczących przechowywania i transportu substancji niebezpiecznych.
Jakie są korzyści ekonomiczne wynikające z efektywnej destylacji rozpuszczalników
Efektywna destylacja rozpuszczalników przynosi wiele korzyści ekonomicznych dla przedsiębiorstw zajmujących się produkcją chemiczną oraz pokrewnymi branżami. Przede wszystkim zwiększa wydajność procesu produkcyjnego poprzez optymalizację wykorzystania surowców oraz minimalizację strat materiałowych. Dzięki zastosowaniu nowoczesnych technologii i automatyzacji możliwe jest osiągnięcie wyższej jakości produktów końcowych, co przekłada się na lepszą konkurencyjność na rynku. Zmniejszenie zużycia energii podczas procesu destylacji również wpływa na obniżenie kosztów operacyjnych przedsiębiorstwa. Dodatkowo, efektywna separacja składników pozwala na odzysk cennych substancji chemicznych, które mogą być ponownie wykorzystane w produkcji lub sprzedane jako surowce wtórne. W dłuższej perspektywie czasowej inwestycje w nowoczesne technologie destylacyjne mogą prowadzić do znacznych oszczędności oraz poprawy rentowności działalności gospodarczej.
Jakie są przyszłe kierunki rozwoju technologii destylacji rozpuszczalników
Przyszłość technologii destylacji rozpuszczalników zapowiada się obiecująco dzięki ciągłemu postępowi naukowemu oraz innowacjom technologicznym. Jednym z głównych kierunków rozwoju jest dalsza automatyzacja procesów produkcyjnych, co pozwoli na jeszcze dokładniejsze monitorowanie parametrów pracy urządzeń oraz szybsze reagowanie na ewentualne problemy. Rozwój sztucznej inteligencji i uczenia maszynowego może przyczynić się do optymalizacji procesów destylacyjnych poprzez analizę danych oraz prognozowanie wydajności różnych metod separacji. Kolejnym ważnym trendem jest poszukiwanie bardziej ekologicznych rozwiązań, takich jak wykorzystanie odnawialnych źródeł energii czy zmniejszenie emisji gazów cieplarnianych związanych z procesem destylacji. Innowacyjne metody separacji, takie jak ekstrakcja superkrytyczna czy wykorzystanie nanotechnologii, mogą stać się alternatywami dla tradycyjnej destylacji i oferować nowe możliwości w zakresie oczyszczania substancji chemicznych.
Jakie są wyzwania związane z destylacją rozpuszczalników w przemyśle
Destylacja rozpuszczalników, mimo swoich licznych zalet, wiąże się także z pewnymi wyzwaniami, które mogą wpływać na jej efektywność oraz bezpieczeństwo. Jednym z głównych problemów jest konieczność ciągłego monitorowania i dostosowywania parametrów procesu, co wymaga zaawansowanego sprzętu oraz odpowiednio przeszkolonego personelu. W przypadku zmieniających się warunków surowcowych, takich jak różnice w składzie mieszanin, może być konieczne dostosowanie technologii destylacji, co generuje dodatkowe koszty. Kolejnym wyzwaniem jest zarządzanie odpadami powstającymi w wyniku procesu destylacji, które mogą zawierać substancje niebezpieczne dla środowiska. Przemysł musi wdrażać skuteczne strategie ich utylizacji oraz minimalizacji ich ilości. Dodatkowo, zmiany regulacyjne dotyczące ochrony środowiska mogą wymuszać na przedsiębiorstwach dostosowanie procesów produkcyjnych do nowych norm, co również wiąże się z dodatkowymi kosztami.