Budowa maszyn roboczych to złożony proces, który wymaga zrozumienia wielu podstawowych elementów. Każda maszyna robocza składa się z kilku kluczowych komponentów, które współpracują ze sobą, aby zapewnić efektywne działanie. Wśród najważniejszych elementów znajdują się napęd, układ sterowania oraz struktura nośna. Napęd jest odpowiedzialny za generowanie energii potrzebnej do pracy maszyny, a jego rodzaj może być różny w zależności od przeznaczenia urządzenia. Układ sterowania z kolei umożliwia operatorowi kontrolowanie pracy maszyny i dostosowywanie jej parametrów do aktualnych potrzeb. Struktura nośna to fundament, na którym opiera się cała konstrukcja, dlatego musi być odpowiednio zaprojektowana, aby wytrzymać obciążenia i zapewnić stabilność. Dodatkowo, w budowie maszyn roboczych istotne są także elementy pomocnicze, takie jak systemy hydrauliczne czy pneumatyczne, które zwiększają funkcjonalność urządzeń i umożliwiają wykonywanie bardziej skomplikowanych zadań.
Jakie są najczęstsze zastosowania maszyn roboczych w przemyśle
Maszyny robocze znajdują szerokie zastosowanie w różnych branżach przemysłowych, co czyni je niezbędnym elementem nowoczesnej produkcji. W sektorze budowlanym maszyny takie jak koparki, ładowarki czy dźwigi odgrywają kluczową rolę w realizacji projektów budowlanych. Dzięki nim możliwe jest szybkie i efektywne wykonywanie prac ziemnych oraz transport materiałów budowlanych. W przemyśle ciężkim natomiast wykorzystuje się maszyny do obróbki metalu, takie jak tokarki czy frezarki, które pozwalają na precyzyjne formowanie różnych komponentów. W rolnictwie maszyny robocze takie jak ciągniki czy kombajny znacznie ułatwiają prace polowe, zwiększając wydajność upraw oraz zbiorów. W przemyśle spożywczym natomiast stosuje się maszyny do pakowania i przetwarzania żywności, co przyczynia się do poprawy jakości produktów oraz ich dłuższej trwałości.
Jakie są nowoczesne technologie w budowie maszyn roboczych
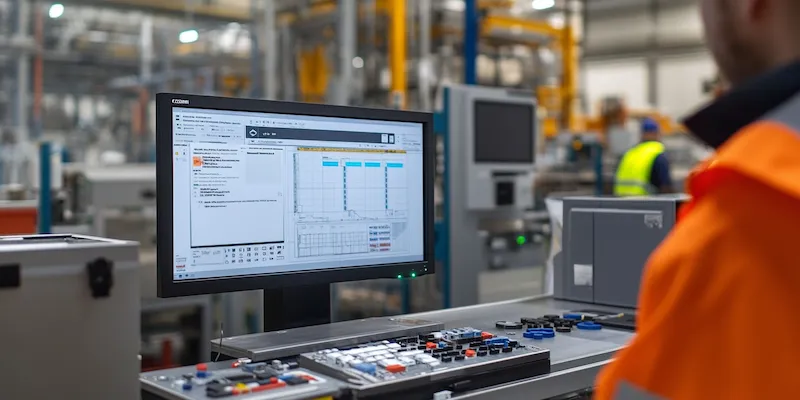
Nowoczesne technologie w budowie maszyn roboczych znacząco zmieniają sposób projektowania i produkcji tych urządzeń. W ostatnich latach obserwuje się dynamiczny rozwój automatyzacji oraz robotyzacji procesów produkcyjnych, co pozwala na zwiększenie efektywności i precyzji działań. Wykorzystanie technologii CAD (Computer-Aided Design) umożliwia inżynierom tworzenie szczegółowych modeli 3D maszyn przed ich fizyczną produkcją, co pozwala na szybsze wykrywanie ewentualnych błędów konstrukcyjnych oraz optymalizację projektu. Dodatkowo, technologie druku 3D zaczynają być coraz częściej wykorzystywane w produkcji części zamiennych do maszyn roboczych, co znacznie skraca czas realizacji zamówień oraz redukuje koszty produkcji. Wprowadzenie systemów IoT (Internet of Things) do maszyn roboczych umożliwia monitorowanie ich stanu w czasie rzeczywistym oraz zdalne zarządzanie ich pracą, co przyczynia się do zwiększenia bezpieczeństwa i niezawodności urządzeń.
Jakie są kluczowe czynniki wpływające na efektywność maszyn roboczych
Efektywność maszyn roboczych jest determinowana przez wiele czynników, które mogą wpływać na ich wydajność oraz niezawodność. Jednym z najważniejszych aspektów jest jakość materiałów użytych do produkcji poszczególnych komponentów maszyny. Wytrzymałe i odporne na zużycie materiały przekładają się na dłuższą żywotność urządzenia oraz mniejsze ryzyko awarii. Kolejnym kluczowym czynnikiem jest odpowiednia konserwacja i serwisowanie maszyn. Regularne przeglądy techniczne oraz wymiana zużytych części pozwalają utrzymać maszyny w dobrym stanie technicznym i zapewniają ich optymalne działanie. Również umiejętności operatora mają ogromne znaczenie dla efektywności pracy maszyny – dobrze przeszkolony personel potrafi maksymalnie wykorzystać możliwości urządzenia oraz unikać błędów mogących prowadzić do uszkodzeń. Oprócz tego warto zwrócić uwagę na ergonomię stanowiska pracy operatora – dobrze zaprojektowane miejsce pracy sprzyja lepszej koncentracji i komfortowi użytkownika, co również wpływa na wydajność całego procesu produkcyjnego.
Jakie są najważniejsze trendy w rozwoju maszyn roboczych
W ostatnich latach można zaobserwować wiele istotnych trendów w rozwoju maszyn roboczych, które mają na celu zwiększenie ich efektywności oraz dostosowanie do zmieniających się potrzeb rynku. Jednym z najważniejszych kierunków jest automatyzacja procesów produkcyjnych, co pozwala na minimalizację błędów ludzkich oraz zwiększenie wydajności. Wprowadzenie robotów przemysłowych do linii produkcyjnych staje się standardem w wielu branżach, a ich zastosowanie przyczynia się do szybszej realizacji zadań oraz obniżenia kosztów pracy. Kolejnym trendem jest rozwój technologii sztucznej inteligencji, która umożliwia maszynom uczenie się na podstawie danych i dostosowywanie swojego działania do zmieniających się warunków. Dzięki temu maszyny mogą pracować bardziej efektywnie, a także przewidywać potencjalne awarie, co pozwala na wcześniejsze podjęcie działań naprawczych. Wzrost znaczenia zrównoważonego rozwoju również wpływa na projektowanie maszyn roboczych – producenci coraz częściej poszukują rozwiązań, które są bardziej ekologiczne i energooszczędne. Wykorzystanie odnawialnych źródeł energii oraz materiałów przyjaznych dla środowiska staje się priorytetem w branży inżynieryjnej.
Jakie są wyzwania w budowie nowoczesnych maszyn roboczych
Budowa nowoczesnych maszyn roboczych wiąże się z wieloma wyzwaniami, które inżynierowie muszą pokonywać, aby sprostać rosnącym wymaganiom rynku. Jednym z głównych problemów jest konieczność ciągłego dostosowywania się do zmieniających się norm i regulacji dotyczących bezpieczeństwa oraz ochrony środowiska. Producenci muszą inwestować w badania i rozwój, aby zapewnić zgodność swoich produktów z obowiązującymi przepisami, co często wiąże się z dodatkowymi kosztami i czasem. Kolejnym wyzwaniem jest szybki postęp technologiczny – aby utrzymać konkurencyjność, firmy muszą nieustannie aktualizować swoje maszyny i wdrażać innowacje. To wymaga nie tylko dużych nakładów finansowych, ale także odpowiednich zasobów ludzkich posiadających wiedzę na temat nowych technologii. Dodatkowo, globalizacja rynku sprawia, że producenci muszą zmagać się z rosnącą konkurencją ze strony firm zagranicznych, co wymusza na nich ciągłe doskonalenie jakości swoich produktów oraz obniżanie kosztów produkcji.
Jakie są kluczowe aspekty projektowania maszyn roboczych
Projektowanie maszyn roboczych to proces wymagający uwzględnienia wielu kluczowych aspektów, które mają wpływ na ich funkcjonalność oraz bezpieczeństwo użytkowania. Przede wszystkim ważne jest określenie przeznaczenia maszyny oraz jej specyfikacji technicznych już na etapie koncepcji. To pozwala na dostosowanie konstrukcji do konkretnych wymagań i warunków pracy. Kolejnym istotnym elementem jest ergonomia – projektanci muszą zadbać o to, aby maszyna była wygodna w obsłudze i minimalizowała ryzyko urazów u operatora. Odpowiednie rozmieszczenie elementów sterujących oraz łatwy dostęp do miejsc konserwacyjnych są kluczowe dla zapewnienia komfortu pracy. Ważnym aspektem jest również analiza kosztów – projektanci muszą znaleźć równowagę między jakością użytych materiałów a ich ceną, aby zapewnić opłacalność produkcji. Dodatkowo, należy uwzględnić możliwość przyszłych modyfikacji maszyny oraz jej serwisowania – elastyczność konstrukcji pozwala na łatwe dostosowanie urządzenia do zmieniających się potrzeb rynku.
Jakie są najczęstsze problemy związane z eksploatacją maszyn roboczych
Eksploatacja maszyn roboczych wiąże się z różnorodnymi problemami, które mogą wpływać na ich wydajność oraz niezawodność. Jednym z najczęstszych problemów jest zużycie części mechanicznych wynikające z intensywnej pracy urządzenia. Regularne użytkowanie prowadzi do naturalnego zużycia elementów takich jak łożyska czy paski napędowe, co może skutkować awarią maszyny lub obniżeniem jej efektywności. Dlatego tak ważne jest przeprowadzanie regularnych przeglądów technicznych oraz konserwacji urządzeń, aby wykrywać ewentualne usterki zanim doprowadzą one do poważniejszych problemów. Innym istotnym zagadnieniem jest niewłaściwe użytkowanie maszyny przez operatora – brak odpowiedniego przeszkolenia lub ignorowanie zasad bezpieczeństwa może prowadzić do uszkodzeń sprzętu oraz zagrożeń dla zdrowia pracowników. Problemy mogą również wynikać z niewłaściwego ustawienia parametrów pracy maszyny – nieodpowiednie wartości prędkości czy ciśnienia mogą prowadzić do obniżenia jakości wykonywanych prac lub zwiększonego zużycia energii. Dodatkowo, czynniki zewnętrzne takie jak warunki atmosferyczne czy jakość surowców również mogą wpływać na działanie maszyn roboczych.
Jakie są przyszłościowe kierunki rozwoju budowy maszyn roboczych
Przyszłość budowy maszyn roboczych zapowiada się niezwykle interesująco dzięki dynamicznemu rozwojowi technologii oraz rosnącym wymaganiom rynku. W nadchodzących latach możemy spodziewać się jeszcze większej automatyzacji procesów produkcyjnych, co będzie miało kluczowe znaczenie dla zwiększenia efektywności i redukcji kosztów pracy. Wprowadzenie sztucznej inteligencji do systemów sterowania maszyn pozwoli na lepsze dostosowanie ich działania do zmieniających się warunków operacyjnych oraz optymalizację procesów produkcyjnych w czasie rzeczywistym. Również rozwój Internetu Rzeczy (IoT) umożliwi zbieranie danych dotyczących pracy maszyn i ich analizy w celu przewidywania awarii oraz planowania konserwacji. Zrównoważony rozwój stanie się kolejnym kluczowym kierunkiem – producenci będą coraz częściej poszukiwać ekologicznych rozwiązań zarówno w zakresie materiałów używanych do budowy maszyn, jak i sposobu ich eksploatacji. Wykorzystanie odnawialnych źródeł energii oraz recykling komponentów stanie się standardem w branży inżynieryjnej. Dodatkowo rozwój technologii druku 3D otworzy nowe możliwości w zakresie produkcji części zamiennych oraz prototypowania nowych rozwiązań konstrukcyjnych.