Destylarki do rozpuszczalników to urządzenia, które odgrywają kluczową rolę w procesach chemicznych oraz przemysłowych. Ich głównym celem jest oddzielanie różnych substancji na podstawie różnic w temperaturze wrzenia. Proces ten polega na podgrzewaniu mieszaniny, co powoduje, że substancje o niższej temperaturze wrzenia parują, a następnie skraplają się w chłodnicy. W ten sposób można uzyskać czystsze frakcje rozpuszczalników, co jest niezwykle istotne w wielu branżach, takich jak farmaceutyka, kosmetyki czy produkcja chemikaliów. Warto zaznaczyć, że destylacja jest jedną z najstarszych metod separacji substancji i pomimo rozwoju nowoczesnych technologii, nadal pozostaje jedną z najskuteczniejszych. W zależności od zastosowania, destylarki mogą być dostosowane do pracy z różnymi rodzajami rozpuszczalników, co zwiększa ich wszechstronność. Oprócz tego, nowoczesne urządzenia często wyposażone są w dodatkowe funkcje, takie jak automatyczne sterowanie temperaturą czy systemy monitorowania jakości destylatu.
Jakie są rodzaje destylarek do rozpuszczalników dostępnych na rynku
Na rynku dostępnych jest wiele różnych typów destylarek do rozpuszczalników, które różnią się zarówno konstrukcją, jak i przeznaczeniem. Najpopularniejsze z nich to destylarki prostoliniowe oraz frakcyjne. Destylarki prostoliniowe są najprostsze w budowie i najczęściej stosowane w laboratoriach do separacji jednego rodzaju substancji. Ich działanie opiera się na prostej zasadzie podgrzewania mieszaniny i zbierania pary. Z kolei destylarki frakcyjne są bardziej skomplikowane i umożliwiają oddzielanie kilku frakcji jednocześnie dzięki zastosowaniu kolumny frakcyjnej. Tego typu urządzenia są szczególnie przydatne w przemyśle petrochemicznym oraz farmaceutycznym, gdzie wymagana jest wysoka jakość końcowego produktu. Innym rodzajem są destylarki próżniowe, które pozwalają na destylację substancji w obniżonym ciśnieniu. Dzięki temu możliwe jest oddzielanie substancji o wysokiej temperaturze wrzenia bez ryzyka ich degradacji.
Jakie zastosowania mają destylarki do rozpuszczalników w przemyśle
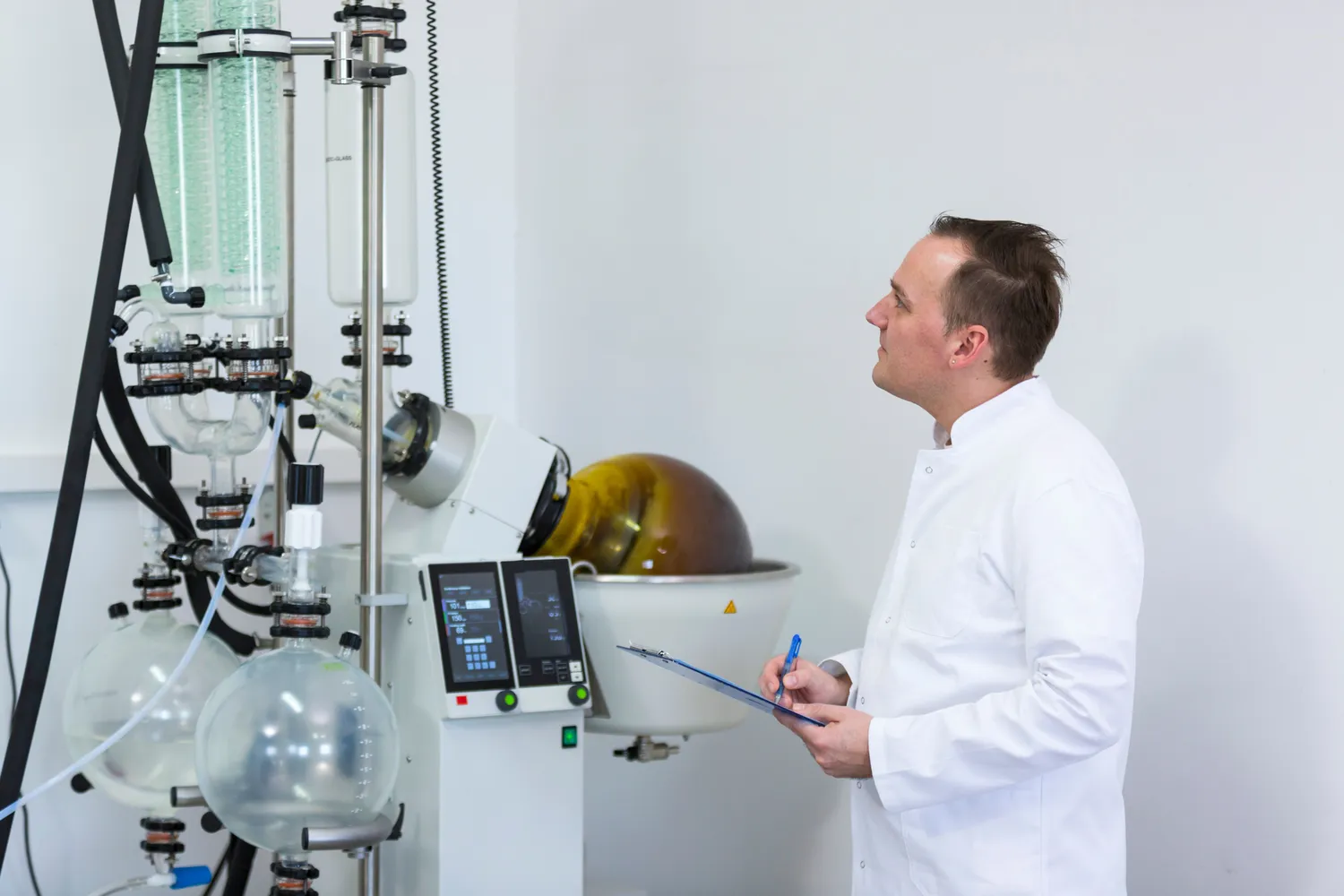
Destylarki do rozpuszczalników znajdują szerokie zastosowanie w różnych gałęziach przemysłu, co czyni je niezwykle ważnym narzędziem w wielu procesach produkcyjnych. W przemyśle chemicznym służą do oczyszczania surowców oraz odzyskiwania cennych rozpuszczalników po zakończeniu procesu produkcji. Dzięki temu możliwe jest nie tylko zwiększenie efektywności produkcji, ale także zmniejszenie kosztów związanych z zakupem nowych surowców. W branży farmaceutycznej destylarki wykorzystywane są do produkcji wysokiej jakości substancji czynnych oraz ich oczyszczania przed dalszymi etapami produkcji leków. Ponadto w przemyśle kosmetycznym destylacja pozwala na uzyskanie czystych olejków eterycznych oraz innych składników aktywnych stosowanych w kosmetykach. Również w przemyśle spożywczym destylarki znajdują swoje miejsce, szczególnie przy produkcji alkoholi oraz aromatów.
Jakie są zalety korzystania z destylarek do rozpuszczalników
Korzystanie z destylarek do rozpuszczalników niesie ze sobą wiele korzyści zarówno dla przedsiębiorstw przemysłowych, jak i dla laboratoriów badawczych. Przede wszystkim umożliwiają one uzyskanie wysokiej czystości produktów końcowych, co jest kluczowe w wielu branżach wymagających spełnienia rygorystycznych norm jakościowych. Dzięki procesowi destylacji można skutecznie oddzielić niepożądane zanieczyszczenia oraz inne substancje chemiczne, co przekłada się na lepszą jakość finalnych produktów. Kolejną zaletą jest możliwość odzyskiwania cennych surowców, co pozwala na zmniejszenie kosztów operacyjnych oraz ograniczenie wpływu na środowisko poprzez redukcję odpadów chemicznych. Dodatkowo nowoczesne destylarki często wyposażone są w zaawansowane systemy monitorowania i automatyzacji procesów, co zwiększa ich efektywność i bezpieczeństwo użytkowania.
Jakie są najczęstsze problemy z destylarkami do rozpuszczalników
Podczas użytkowania destylarek do rozpuszczalników mogą wystąpić różne problemy, które mogą wpłynąć na efektywność procesu oraz jakość uzyskiwanego produktu. Jednym z najczęstszych problemów jest niewłaściwe ustawienie temperatury, co może prowadzić do niepełnej destylacji lub przegrzewania substancji. W przypadku zbyt wysokiej temperatury istnieje ryzyko degradacji cennych składników, co negatywnie wpływa na jakość końcowego produktu. Innym istotnym problemem jest zatykanie się kolumny frakcyjnej, co może być spowodowane osadzaniem się zanieczyszczeń lub nieodpowiednią jakością surowców. Zatykanie kolumny prowadzi do obniżenia wydajności destylacji oraz zwiększa ryzyko awarii urządzenia. Warto również zwrócić uwagę na system chłodzenia, który ma kluczowe znaczenie dla prawidłowego przebiegu procesu. Niewłaściwe działanie chłodnicy może prowadzić do utraty pary i obniżenia efektywności separacji.
Jakie czynniki wpływają na wybór destylarki do rozpuszczalników
Wybór odpowiedniej destylarki do rozpuszczalników powinien być dokładnie przemyślany, ponieważ wiele czynników wpływa na efektywność i jakość procesu destylacji. Przede wszystkim należy zwrócić uwagę na rodzaj rozpuszczalnika, który będzie poddawany destylacji. Różne substancje mają różne temperatury wrzenia, co może wymagać zastosowania specyficznych typów destylarek, takich jak destylarki próżniowe czy frakcyjne. Kolejnym istotnym czynnikiem jest skala produkcji – w przypadku dużych zakładów przemysłowych konieczne mogą być bardziej zaawansowane technologicznie urządzenia o dużej wydajności, podczas gdy w laboratoriach wystarczą mniejsze i prostsze modele. Ważnym aspektem jest także budżet przeznaczony na zakup destylarki oraz koszty eksploatacji związane z jej użytkowaniem. Należy również uwzględnić dostępność serwisu oraz części zamiennych, co ma kluczowe znaczenie dla długotrwałego użytkowania urządzenia.
Jakie są różnice między destylacją prostą a frakcyjną
Destylacja prosta i frakcyjna to dwa podstawowe procesy stosowane w destylacji rozpuszczalników, które różnią się zarówno zasadą działania, jak i zastosowaniem. Destylacja prosta polega na podgrzewaniu mieszaniny do momentu, gdy substancja o niższej temperaturze wrzenia zaczyna parować. Para ta następnie skrapla się w chłodnicy i zbiera w osobnym naczyniu. Proces ten jest stosunkowo prosty i szybki, jednak ma swoje ograniczenia – nie jest w stanie skutecznie oddzielić substancji o zbliżonych temperaturach wrzenia. Z tego powodu najczęściej stosuje się go do oczyszczania jednego rodzaju substancji lub przy separacji substancji o znacznie różniących się temperaturach wrzenia. Z kolei destylacja frakcyjna jest bardziej skomplikowanym procesem, który wykorzystuje kolumnę frakcyjną do oddzielania kilku frakcji jednocześnie. Dzięki temu możliwe jest uzyskanie wyższej czystości produktów oraz lepsza separacja substancji o zbliżonych temperaturach wrzenia.
Jakie innowacje technologiczne wpływają na rozwój destylarek do rozpuszczalników
W ostatnich latach branża technologii chemicznej przeżywa dynamiczny rozwój, co ma bezpośredni wpływ na konstrukcję i funkcjonalność destylarek do rozpuszczalników. Innowacje technologiczne obejmują m.in. automatyzację procesów oraz zastosowanie nowoczesnych systemów monitorowania, które pozwalają na precyzyjne kontrolowanie parametrów pracy urządzenia. Dzięki tym rozwiązaniom operatorzy mogą skuteczniej zarządzać procesem destylacji, minimalizując ryzyko błędów ludzkich oraz zwiększając efektywność produkcji. Ponadto rozwój materiałów i technologii produkcji umożliwia tworzenie bardziej trwałych i odpornych na korozję elementów destylarek, co przekłada się na ich dłuższą żywotność oraz mniejsze koszty eksploatacji. Warto również zwrócić uwagę na rosnącą popularność ekologicznych rozwiązań w przemyśle chemicznym, co prowadzi do projektowania urządzeń o niższym zużyciu energii oraz mniejszym wpływie na środowisko naturalne.
Jakie są kluczowe aspekty bezpieczeństwa przy używaniu destylarek
Bezpieczeństwo podczas użytkowania destylarek do rozpuszczalników jest niezwykle istotne ze względu na potencjalne zagrożenia związane z pracą z substancjami chemicznymi oraz wysokimi temperaturami. Kluczowym aspektem jest zapewnienie odpowiedniej wentylacji w pomieszczeniu, w którym znajduje się destylarka, aby uniknąć gromadzenia się szkodliwych oparów chemicznych. Użytkownicy powinni być również dobrze przeszkoleni w zakresie obsługi urządzenia oraz znajomości procedur awaryjnych, aby móc szybko reagować w przypadku wystąpienia nieprzewidzianych sytuacji. Ważne jest także regularne przeprowadzanie konserwacji i inspekcji technicznych urządzeń, aby upewnić się, że wszystkie elementy działają prawidłowo i nie stwarzają zagrożeń dla zdrowia i życia pracowników. Dodatkowo stosowanie odpowiednich środków ochrony osobistej, takich jak rękawice czy okulary ochronne, jest niezbędne podczas pracy z substancjami chemicznymi oraz przy obsłudze sprzętu generującego wysokie temperatury.
Jakie są przyszłe kierunki rozwoju technologii destylacji
Przyszłość technologii destylacji zapowiada się obiecująco dzięki ciągłemu postępowi naukowemu oraz technologicznemu w dziedzinie chemii i inżynierii procesowej. Wśród najważniejszych trendów można zauważyć rosnącą tendencję do automatyzacji procesów produkcyjnych oraz integracji systemów informatycznych z urządzeniami przemysłowymi. Dzięki temu możliwe będzie uzyskanie jeszcze większej precyzji w kontrolowaniu parametrów pracy destylarek oraz szybsze reagowanie na zmiany zachodzące podczas procesu. Kolejnym kierunkiem rozwoju jest poszukiwanie bardziej ekologicznych metod separacji substancji chemicznych, które będą miały mniejszy wpływ na środowisko naturalne oraz będą bardziej energooszczędne. W miarę jak rośnie świadomość ekologiczna społeczeństwa oraz regulacje dotyczące ochrony środowiska stają się coraz bardziej rygorystyczne, branża chemiczna będzie musiała dostosować swoje technologie do tych wymagań.